Module ‘Sandwich’ Review
It does just happen sometimes… Crashing down from the second floor, broken crystal everywhere. The Swiss Urwerk 103 is a robust and well-constructed watch, but down from the second floor is a hard fall. The sapphire glass is shattered, a strap stud is broken, and the movement has stopped.

URWERK 103 limited model in white gold. Full repair official statement was £4K+…
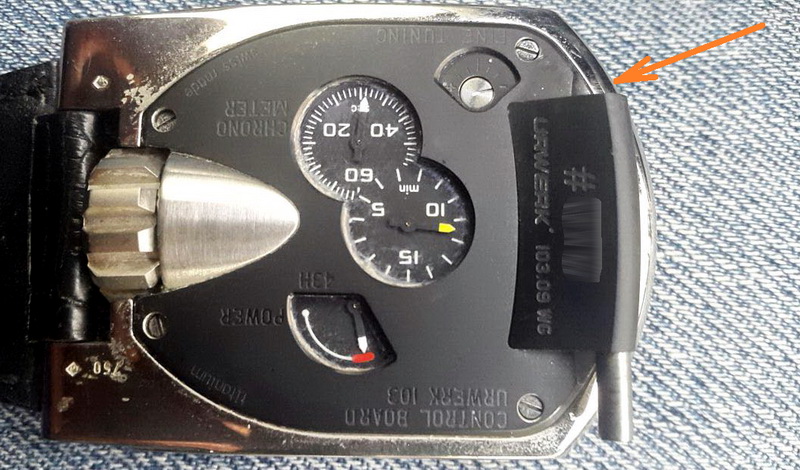
The strap holding stud has broken off.
First of all, we took the watch apart to check for hidden damages and to clean all the glass micro-shards out. The movement needs to be fully disassembled and cleaned too, as broken sapphire particles can cause a lot of damage to cogs and pivots, potentially leading to multiple scratches, as well as causing the movement to wear out after only a few days of running.
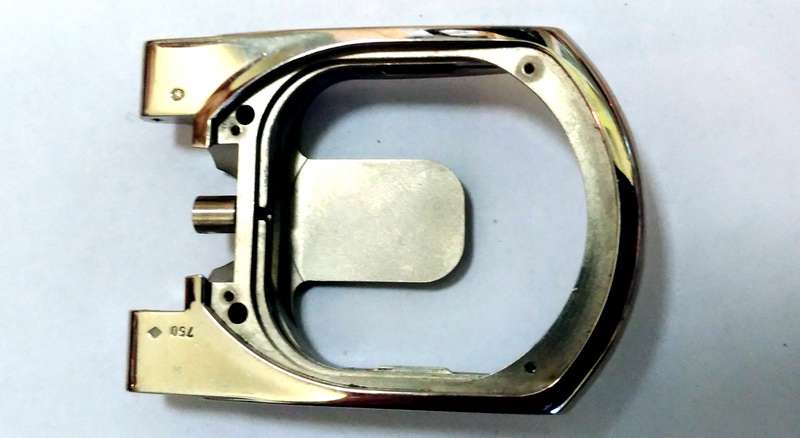
The watch is taken apart for cleaning and washed thoroughly to rid it of glass micro-shards. Then the case must be polished, piece by piece.
URWERK UR-103 ‘Sandwich’ Module
Take a look inside the manufactured caliber, which can’t be seen in general reviews and catalogues.
At the beginning of the brand’s career, their whole idea was based upon the standard ETA 7001 Peseux Swiss movement. This decision was nice, as it was easy to start up and not to be distracted with constructing ultra-precise escapement parts. The engineers focused on the complication, and they did the job very well.
It’s worth pointing out the fact that, in the later models, the creators of the URWERK watch fully integrated the mechanism and constructed completely in-house caliber. This makes the 103 model even more interesting, as it shows off just how the engineers must have been thinking.
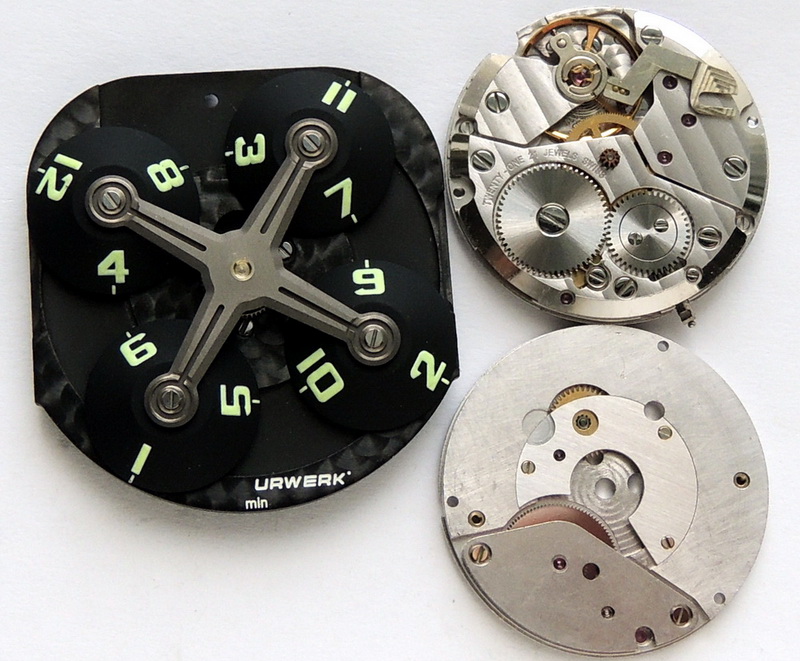
The 103 caliber consists of three interconnected modules, each module is essentially a separate appliance. The indication module shows digital coned discs on a carriage. The carriage is slowly turned by the main 7001 movement, and the coned discs show the current time. The back mounted module is for power reserve indication.

The carriage is mounted on ball bearings, and the Maltese cross pieces interact with the switch pin.
The principal of numeral disc switching is based on the Maltese cross – a classical mechanical device. In the UR-103 it is implemented slightly inside out: the cross rotates around the carriage centre and is switched with a steel pin fixed in the main-plate (see blue arrows in above picture for reference).
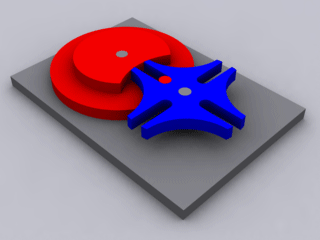
The carriage makes one full rotation every 4 hours, you can see how the module works in the video linked below:
The base movement is connected to the indication module in an upside-down position, and the pinion is added to the centre wheel from the back.
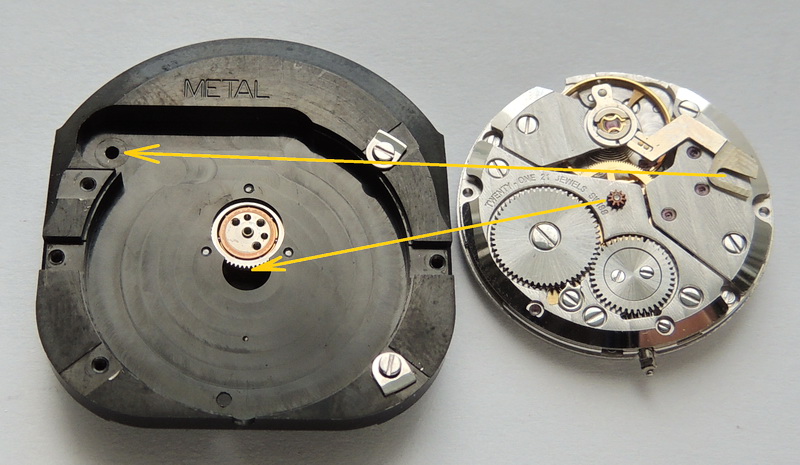
Reduction 4:1, the wheel transforms the power to the necessary one turn per 4 hours, increasing the power for driving the whole carriage rather than just the thin hands.
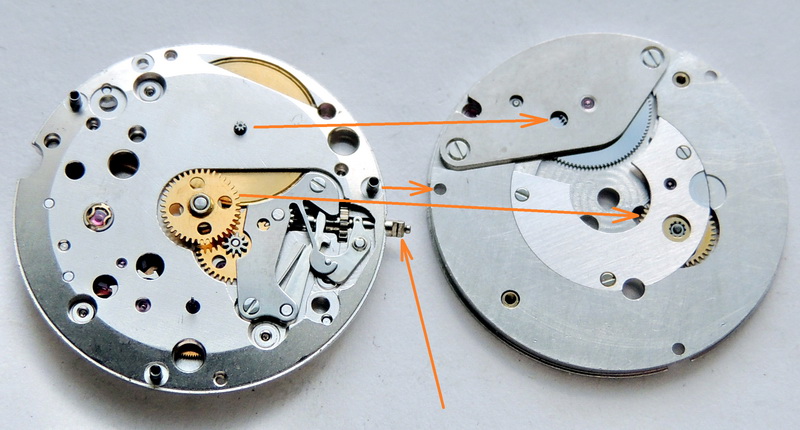
From the front, the basix Peseux movement is modified for power reserve counting.
Now back to the watch repair.
Fortunately, there wasn’t anything inside the movement that was completely unfixable. The modules absorbed the shock, and only one boss-axis was broken. Thus, the UR-103 has proved itself to be a pretty reliable and robust caliber!
It was much more fascinating to find out how the new glass would be made for the complex case shape.
Making the Urwerk Crystal
Because of the high price of repair at an official service (as well as the shipment delays), we finally came around to the idea of making the glass from mineral, not sapphire. Obviously, mineral glass can be scratched much more easily, but with careful handling it will last for just as long. With this route there is also the benefit of being able to polish the mineral to get rid of any scratches. Mineral glass is just as brittle as sapphire, so the chances of it breaking in another incident are equal to before this break. The owner told us to go ahead with the mineral glass, so go ahead we did.
First of all, we measured the curve of the glass inside the case. A rough part is then cut out of a spherical mineral crystal blank.
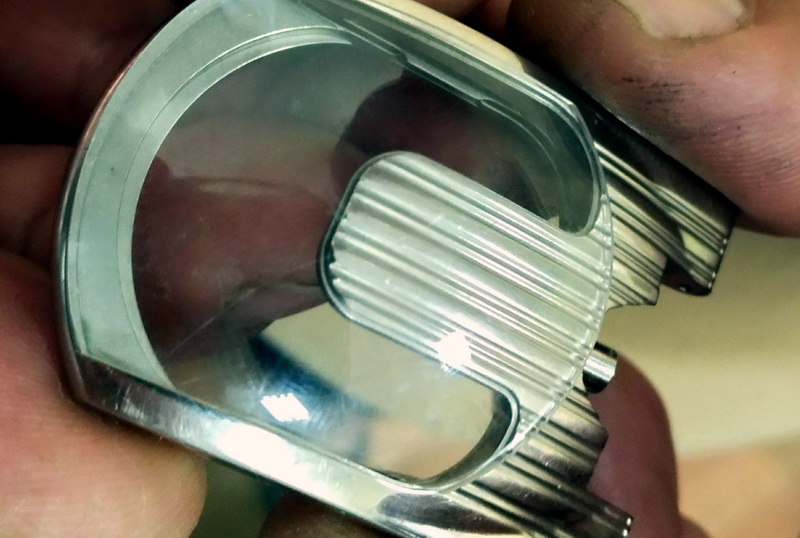
The shaped glass is cut out and checked to see how well it will fit. Extra material is left, which will be polished off later.
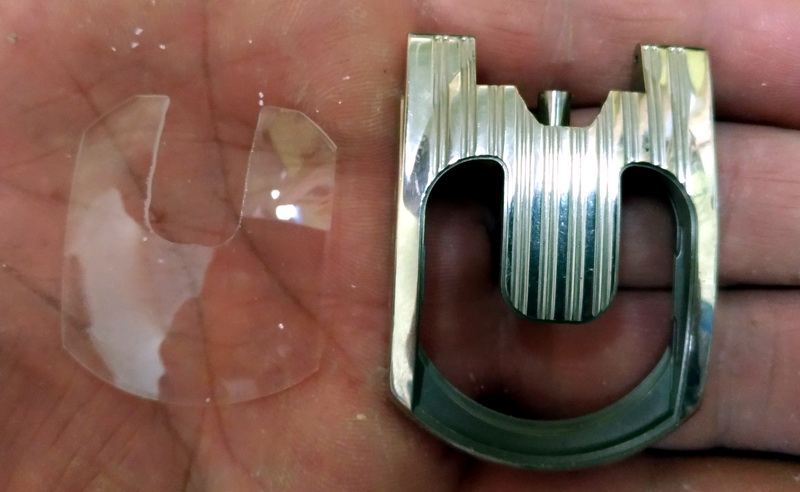
Next, we raw cut material off the middle of the rough part.
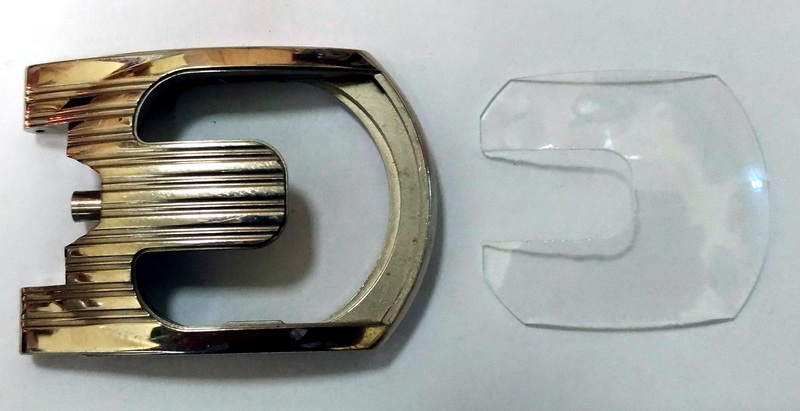
Gradually, the shape begins to look more like the shape that we want to end up with.
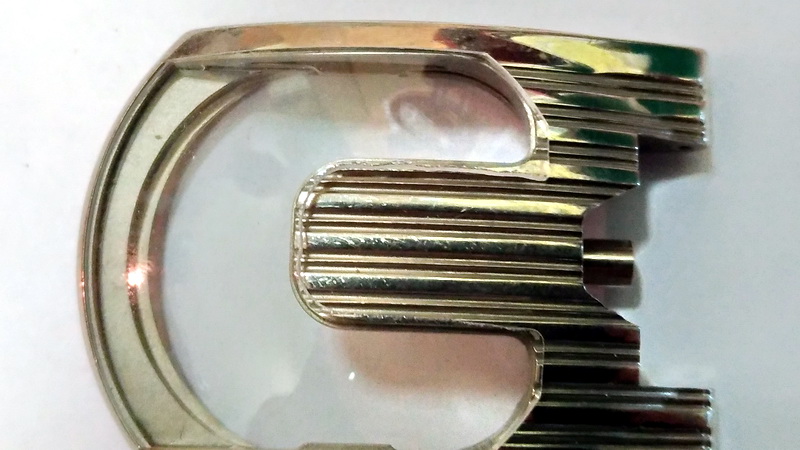
We will still need to cut and polish off some of the edges, to ensure that we get a perfectly flat surface.
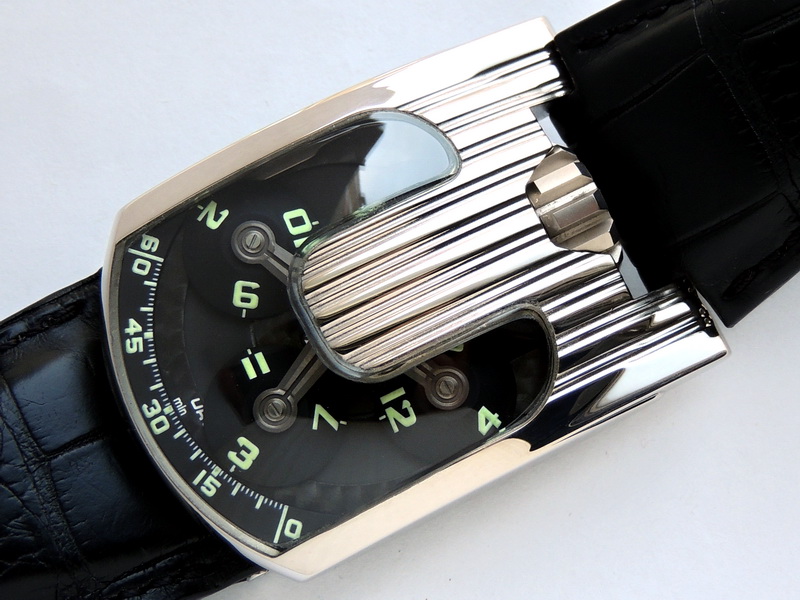
The edges have been adjusted and polished, and the new glass looks right in the case.
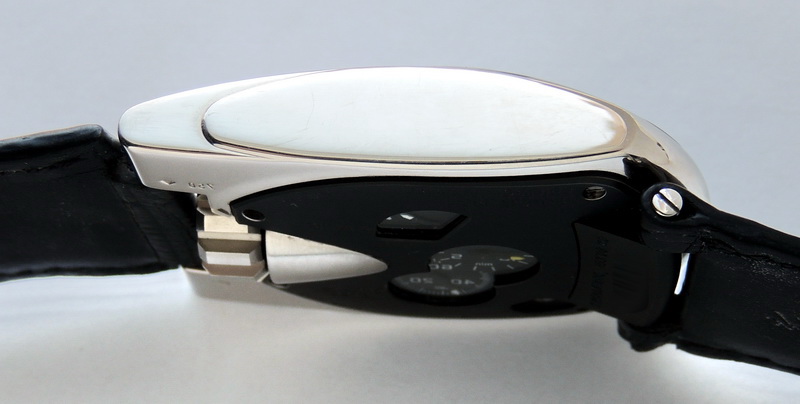
The case has also been polished and buffed, and the scratches have been taken off. The new strap stud was really the easiest piece of work here, as we just machined it with the lathe.
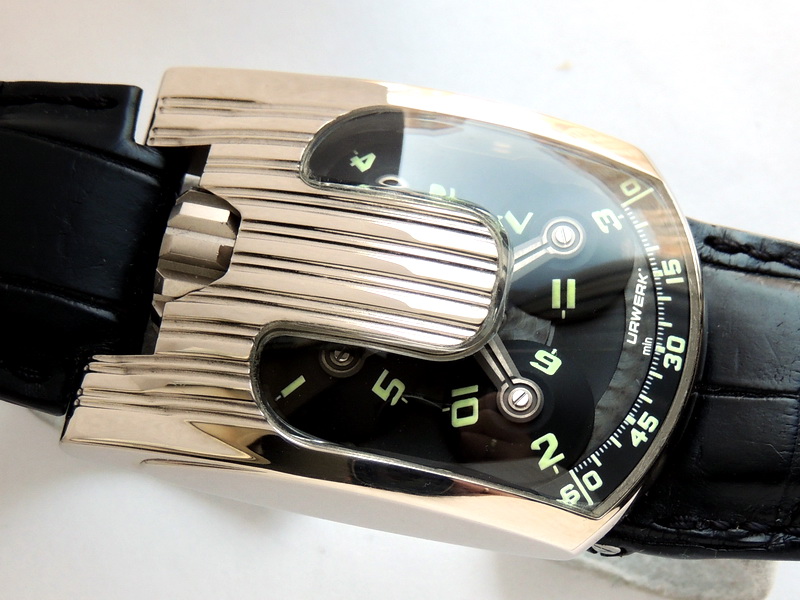
I loved the ‘sandwich’ construction of the movement, the modules are well built, with an easy repairability and great quality joints.
Viva URWERK !!!!